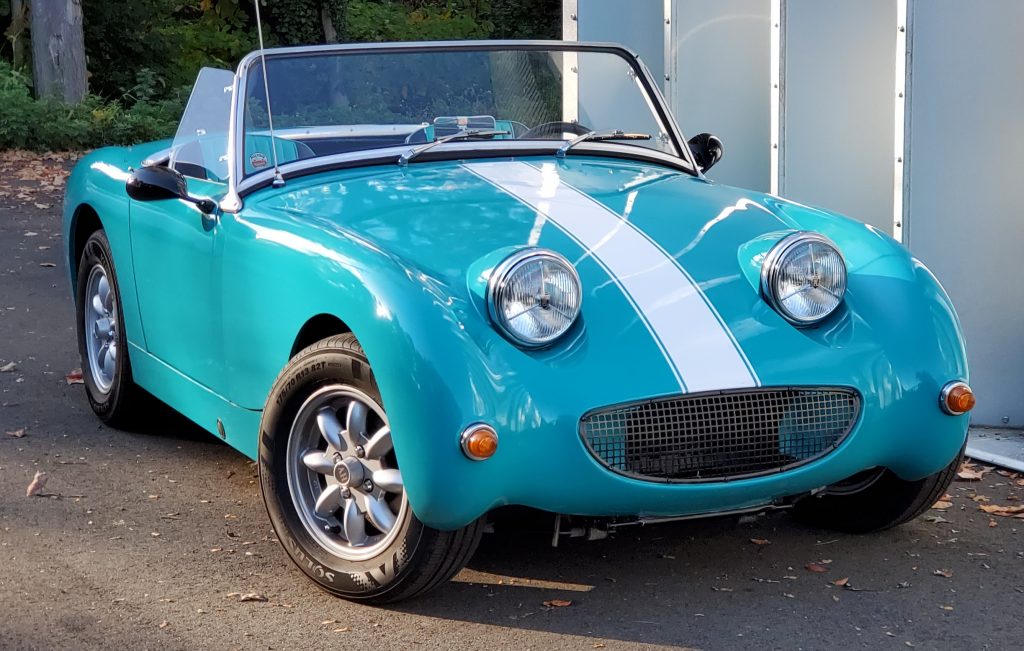
We spend a remarkable amount of time working on Bugeye noses. One cannot handle more than 500 Frogeyes without becoming a nose master… none of them fit. All of them need help. All of them have had some form of trauma. We are forever adjusting and refitting them.
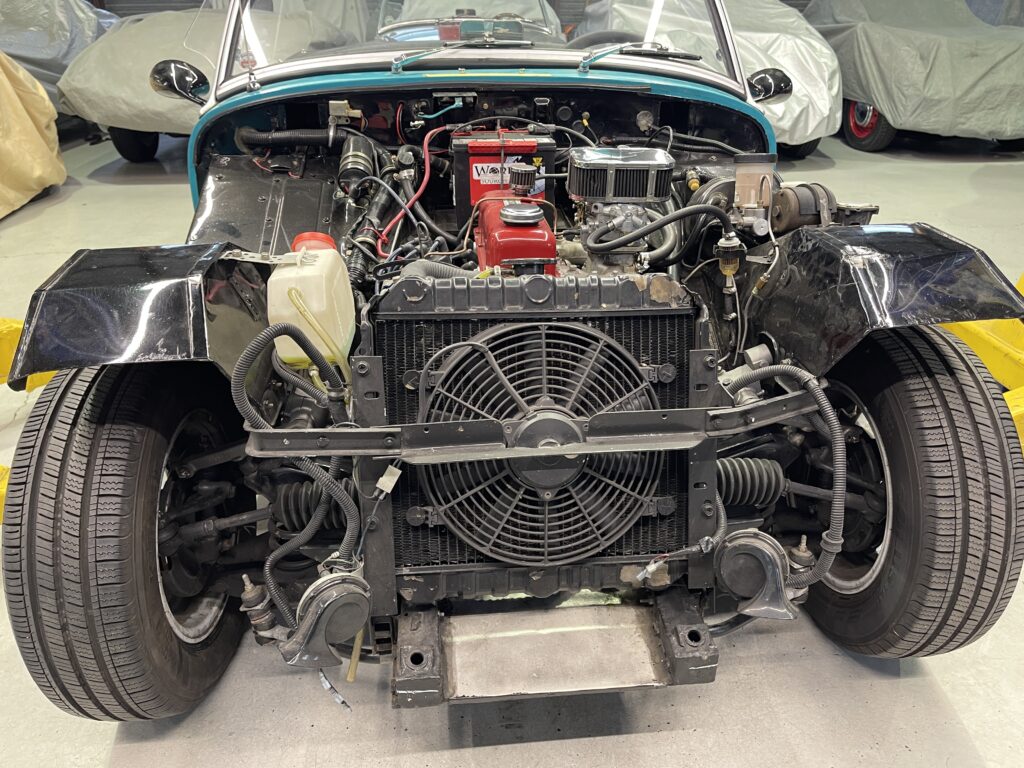
The flip forward option is a delightful innovation, especially for our aging lower backs that enjoy the relative ease with which flip-forward noses flip. It’s a lot less work to flip a nose than hoisting one with conventional hinges. And with flip nose conversions come a set of new challenges… frame horns have to be parallel and we are frequently re-aligning those too.
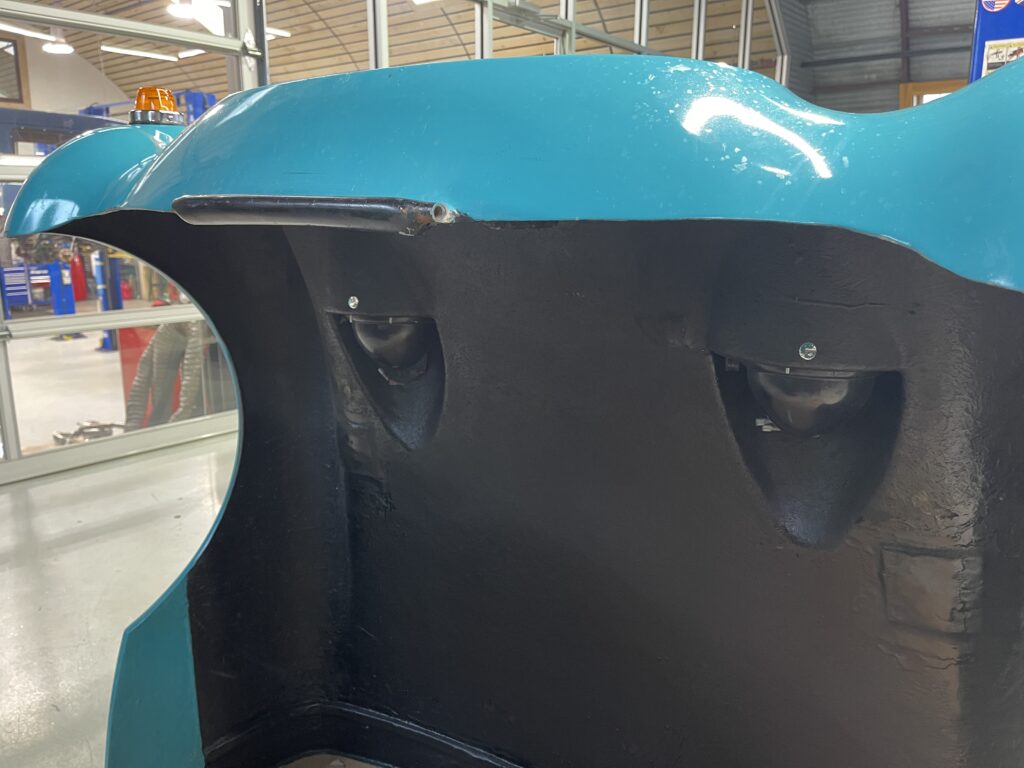
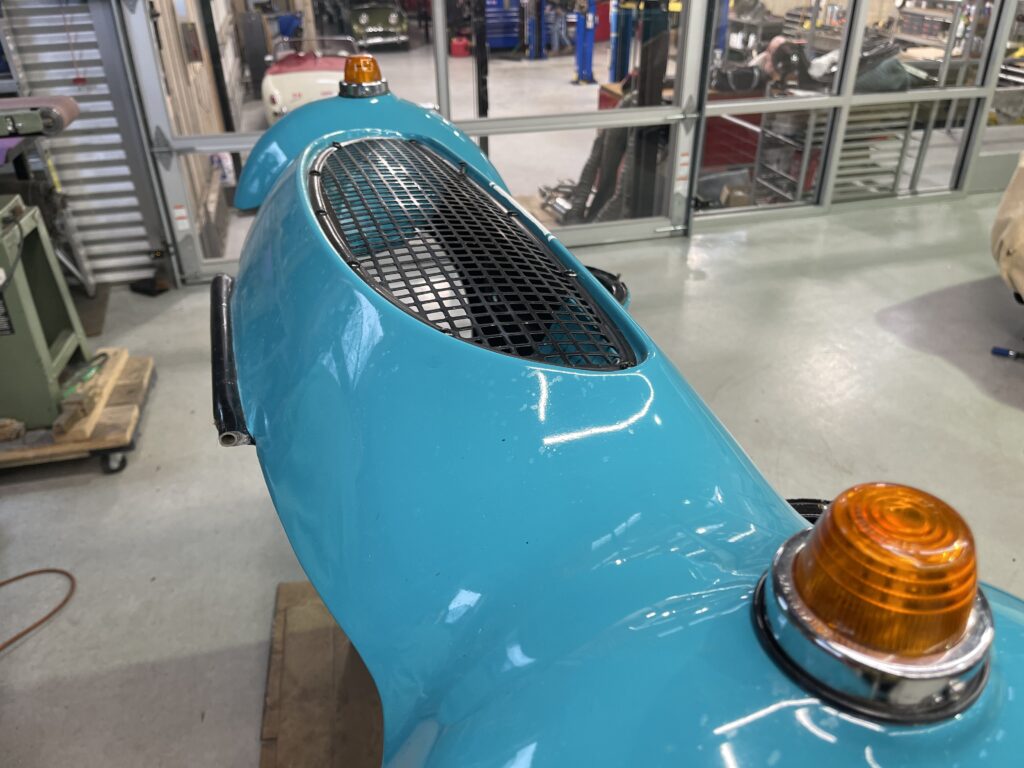
In the pictures here or you see another unique nose challenge. This is a fiberglass nose (on the teal car “Priscilla“) with minimal structure, which made for a very floppy taco shell. We are gifted to have Ken on staff who is a master fabricator, and he constructed a gorgeous inner superstructure to give this droopy nose much more rigidity. In these photos, you can see the initial templates he made for the panels he cut to make a new radiator shroud, thereby adding structural integrity to a nose that was pretty much just flapping in the breeze.
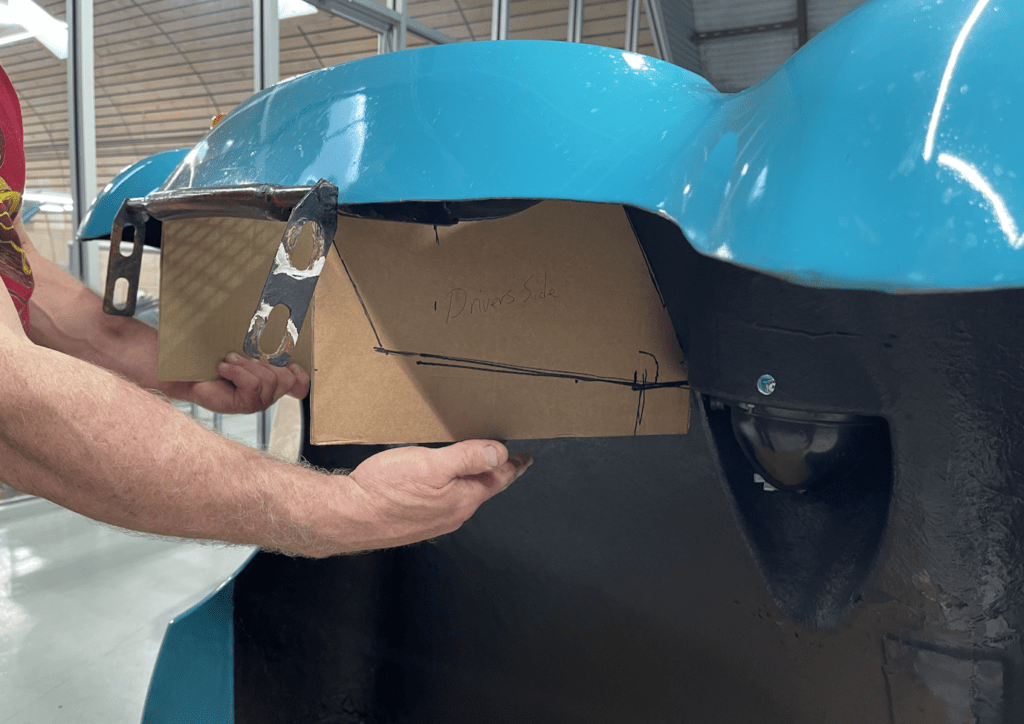
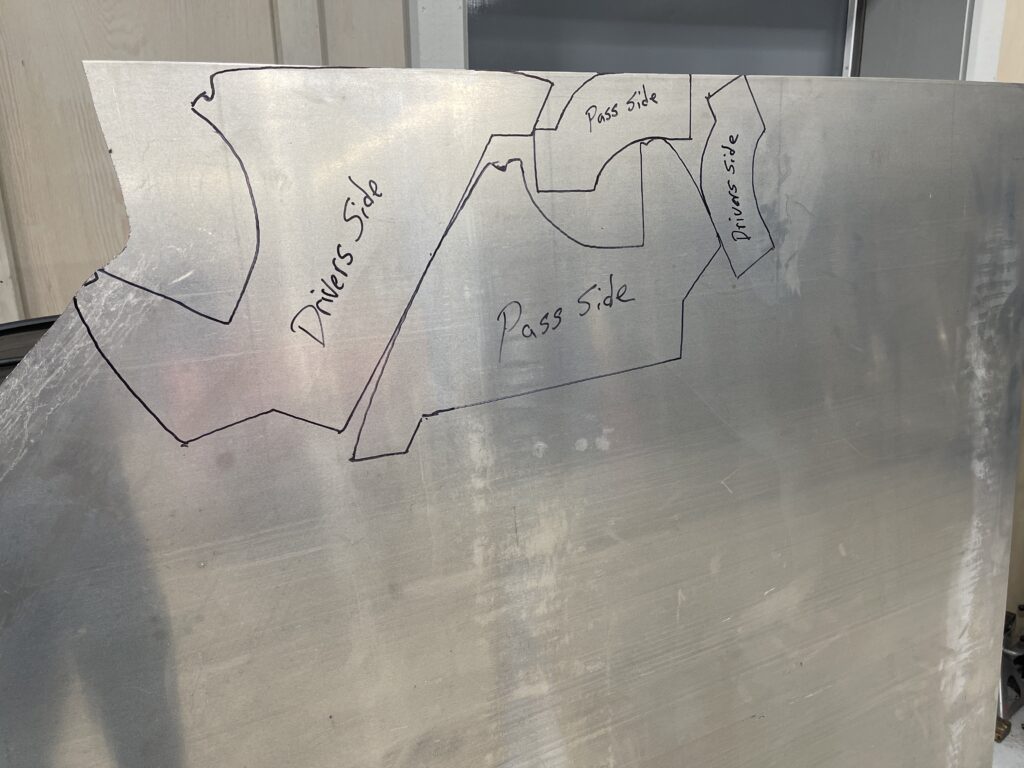
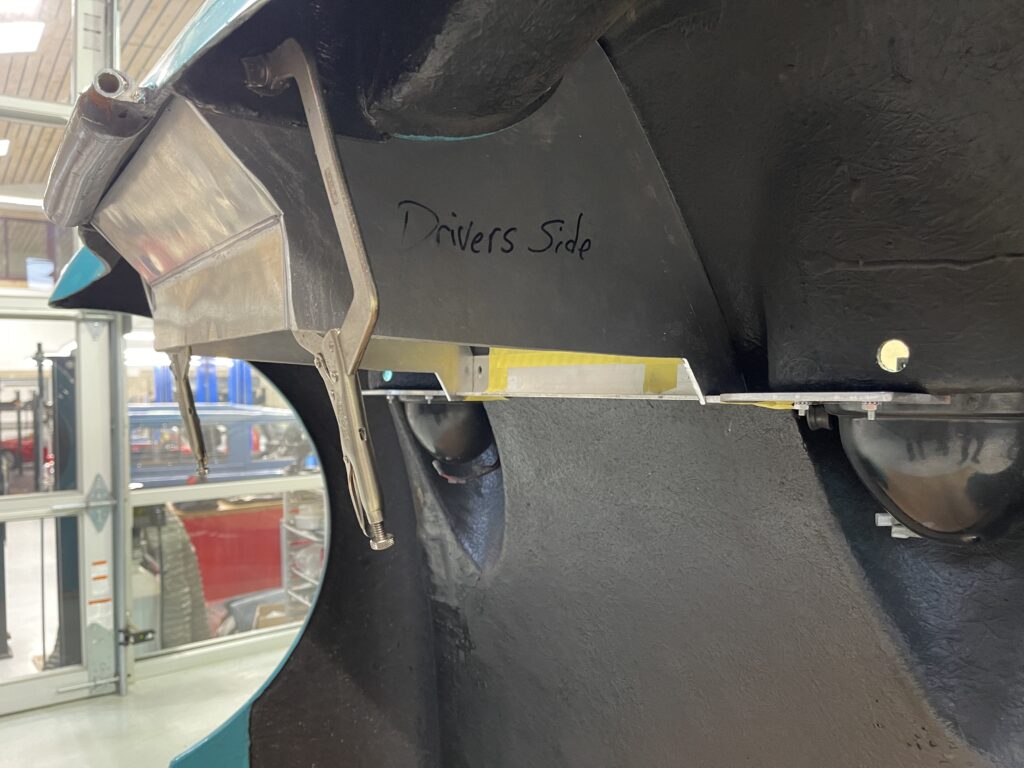
I am beaming to see this innovative repair… we faced a complex challenge to add more rigidity to a wiggly piece of fiberglass in order to better control the nose fit. And now, with Ken’s help, we forged a solution and thus now have the means to fine tune this nose and control its movement. Now, this nose has a fan shroud structure to add much-needed rigidity.
Another Bugeye has now been transformed!
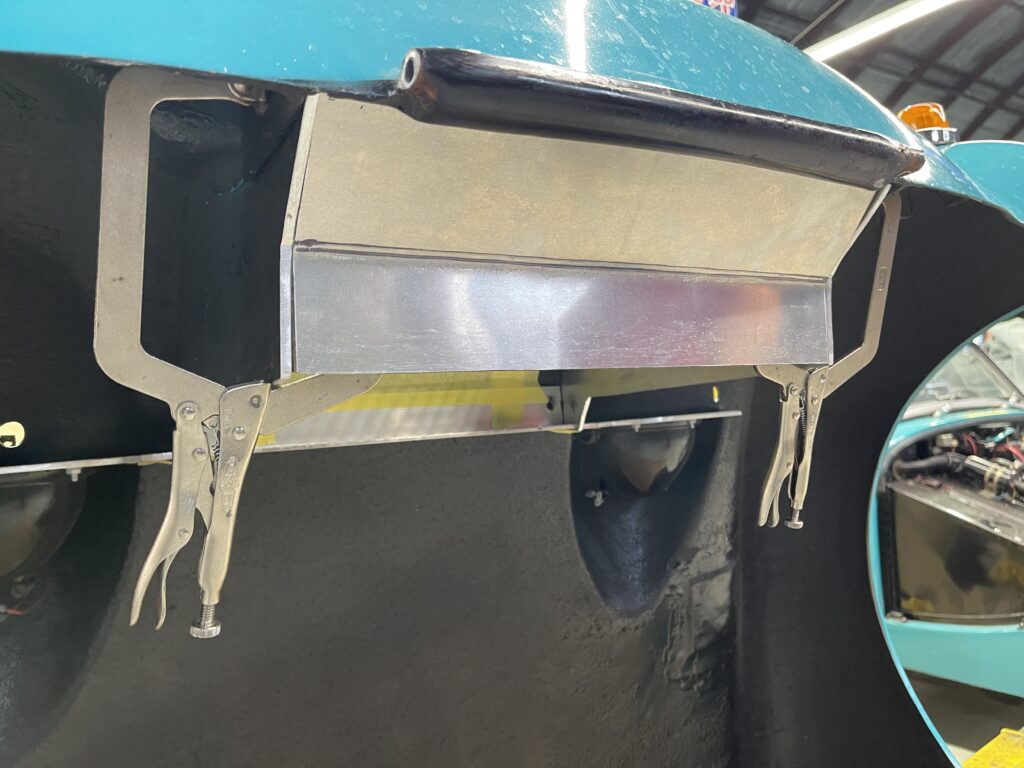
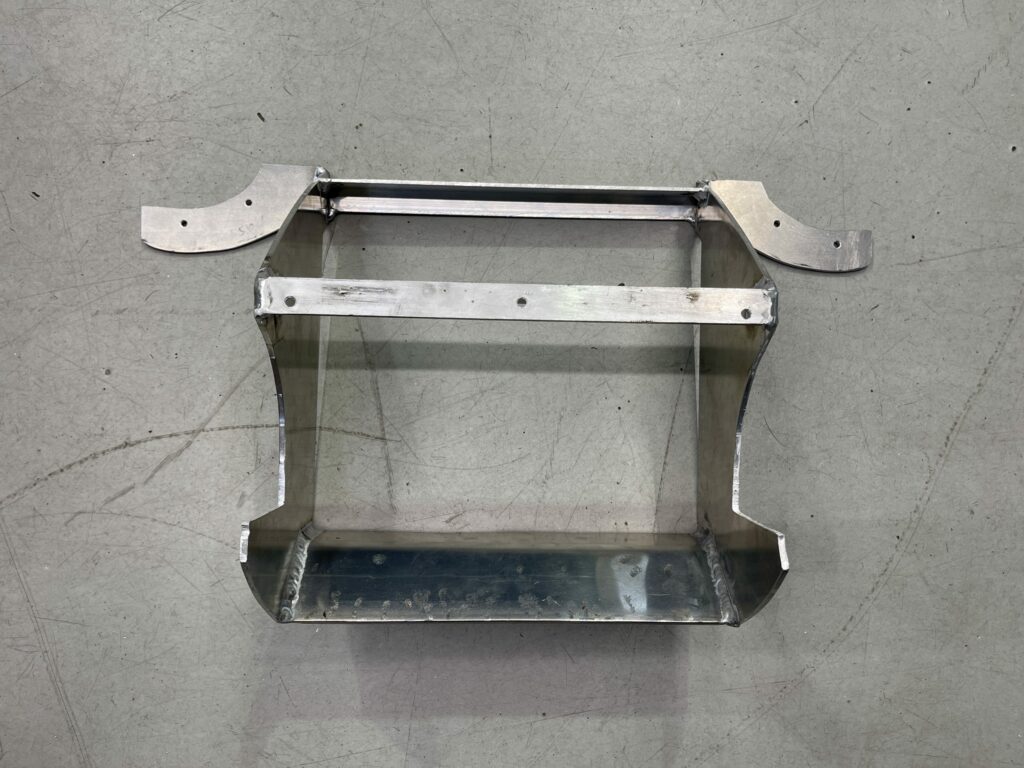